|
|
|
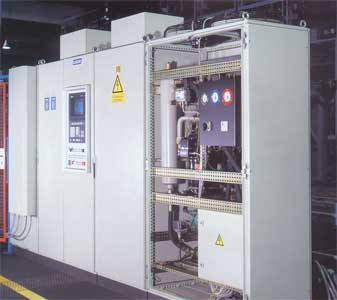 AGC轧机自动液压厚度计算控制系统
一.概述
黑色和有色的板带材用户随着市场需求对板带产品的规格和质量都提出了更高要求,板带加工厂的工艺装备要能满足多规格、高精度、高效率的生产需求,而其主要设备液压轧机的自动化控制水平却严重制约着轧制的产品精度和生产率。
现代化轧机的水平主要体现在能实现高速轧制、高精度的厚度公差、良好的板形、高的生产率的产品等,其控制系统应能够提供多种手段来满足上述的要求。本公司开发的AGC计算机控制系统为用户提供了全面解决方案。
二.控制系统的配置方案
AGC采用上、下位两级计算机控制方案,是集轧机过程控制、过程管理、AGC控制和故障报警诊断为一体的计算机系统。上位机由轧制过程管理计算机(网络服务器)组成:下位机由辊缝控制计算机、厚度控制计算机完成实时控制,配置多台独立的显示操作站(人机界面MMI),并与轧机PLC联网,组成液压轧机的整体自动化系统。。
1. 通讯网络:上、下位机之间的数据通信采用以太网(Ethernet),开放式网络结构,TCP/IP网络通讯协议。采用Windows NT网络操作系统。
2. 计算机配置:所有计算机均选用PC总线PentiumⅢ以上档次的工业控制计算机。其中轧制过程管理计算机采用PentiumⅢ、128MRAM的研华IPC-610工业控制计算机。
3. 工程师台:轧制过程管理计算机、打印机。
4. 控制柜:分AGC计算机柜和AGC接线端子柜。19〞上架结构,内配一个显示器和一个键盘。
5. 机前操作箱:轧机左右侧各设置一机前操作箱,分别安装左右机前触摸计算机。
基于上述硬件配置的软件系统是集轧制过程控制和自动厚度控制为一体的模块化软件系统,由辊缝控制程序、厚度控制程序、轧制过程管理程序、数据显示及操作控制程序、故障诊断及远程诊断等应用程序组成。全部应用程序基于美国微软最新的网络操作系统Windows NT下,采用微软最新的软件开发工具Visual Basic和Visual C++编写,运行于WINDOWS 环境下,软件维护非常方便。同时,整个系统非常便于今后的软硬件升级。
三.轧机数学模型的使用
液压轧机是一个非常复杂的多变量系统,影响产品精度的因素相当多,而且各变量之间存在着耦合关系,即使在恒辊缝轧制的情况下,由于轧制速度、弯辊力、带材入口厚度、冷却、调偏量的变化,也会使得出口厚度目标值发生偏差。传统的做法是使用厚度监控来校正这些偏差,但由于厚度监控周期不可能很快,因此,会不可避免地降低了控制精度,尤其对于高速、薄带轧机。轧机数学模型决定了轧机辊缝、轧制力、弯辊力、轧制速度、轧制力矩、冷却等参数之间的关系,在实际控制过程中,适时、适量的调整及补偿,可以减少上述偏差的出现,进而提高控制精度。
四.带材厚度控制
1. 辊缝控制。辊缝控制是AGC控制的基本内环,它与其他AGC模式一起使用。辊缝位置的检测有若干种选择,位移传感器可安装在轧机压上油缸上、轧机弯辊油缸内或专门设计的检测支座上。在轧机的操作侧和传动分别有两个或两组传感器获取位置反馈信号,然后把这两个信号加以平均产生一个代表中央位置的信号,这个平均值和一个辊缝给定信号相比较,用两者的差值来驱动伺服阀,调整压上油缸使差值趋于零。
2. 压力控制。压力控制是AGC控制的第二个基本内环,它也需与其他AGC模式一起使用。安装于压上油缸上的压力传感器检测油缸内的压力,经转换得到轧机轧制力反馈信号,这个信号和一个压力给定信号相比较,用两者的差值来驱动伺服阀,调整压上油缸使差值趋于零。压力控制主要用于压力-张力速度AGC控制、轧机预压靠调零、轧机调试及故障诊断。
3. 压力AGC控制(GMTR)。这种控制也被称为液压轧机的可变刚性。压力AGC控制可以有效地增加轧机刚性,使轧机的等效刚性远大于轧机的自然刚性。在轧制过程中,控制系统分别检测轧机操作侧和传动侧的轧制压力,根据轧机的刚性曲线,计算出轧制力所引起的机架拉伸,相对于预计机架拉伸的任何变化被送入辊缝控制环进行动态补偿。如果上述变化被完全补偿,即100%补偿,则轧机将呈现一无限大刚性,轧辊辊缝将不受来料厚度和硬度的影响,可以产生恒定的出口厚度。但是,100%轧机刚性补偿会使支承辊偏心完全反映在带材上,同时系统极不稳定,影响轧制精度,实际工作中,补偿的百分比需要调整以获得最佳的轧机性能。
4. 支承辊偏心补偿。在轧制0.1~0.2 mm以上带材,使用;辊缝控制时有效。采用快速傅立叶变换寻找上、下支承辊偏心的分布情况,在实际控制时对偏心进行补偿。
5. 厚度监控。通过出口侧测厚仪检测轧机出口侧带材的厚度偏差,控制轧辊辊缝或轧制压力,使厚度偏差趋于零。厚度监控可以消除因热膨胀、轧制速度等对出口厚度的影响,消除入口厚度变化和入口带材硬度变化的影响。
6. 厚度预控。通过入口侧测厚仪检测轧机入口侧带材厚度,存入一先入先出的厚度链表中,经过延时,根据所存厚度值控制轧辊辊缝或轧制压力,使轧机出口侧带材的厚度偏差减小。延时的时间决定于入口测厚仪至轧辊中心线的距离和轧材的线速度。
7. 秒流量控制。根据流量恒定原理,单位时间内进入轧机的带材体积应等于轧机出口带材的体积,因此,可通过测量轧机入口、出口速度和入口厚度计算出轧机出口厚度,这一计算厚度与设定厚度的偏差用于控制轧辊辊缝或轧制压力,同时,用出口测厚仪测得的带材实际厚度偏差对上述控制进行校正。
8. 张力/速度AGC。张力AGC是通过调整轧机的入口张力,使轧机出口侧带材的厚度偏差趋于零。速度AGC是通过调整轧机的轧制速度,使轧机出口侧带材的厚度偏差趋于零。压力、张力、速度控制的最有效范围如下:
压力控制 0.18~0.09㎜
张力控制 0.09~0.025㎜
速度控制 0.025㎜以下
9.多级AGC。设置有两级控制器进行AGC控制,第一级控制器根据口厚度偏差进行控制,当第一级的被控参数超过预设定的极限值时,启动第二级控制器,同时调整第一、第二级的被控参数,直至第一级的被控参数返回到极限值以内。有四种基本控制模式:压力/张力、张力/压力、速度/张力、张力/速度。
五.带材板形控制
带材板形控制是国产轧机急需解决的一个主要问题,其难点在于板形仪。进口的板形仪价格相当昂贵,为了解决这一难题,国内许多单位正在积极研制板形仪。在目前国产轧机普遍缺少板形仪的情况下,带材板形控制均采用人工目测调整的方法。目前,我们正也在开展板形控制算法的研究,主要思路是采用模糊控制及神经元网络等先进的控制方法,解决板形控制中的多变量时变问题。AGC可以提供下列三种板形控制手段:
1. 正、负弯辊控制。通过调整弯辊力,改变轧辊的弯曲度。主要解决带中部和双边波浪。
2. 辊缝和压力调偏控制。通过分别调整操作侧、传动侧轧辊辊缝,使轧倾斜。主要解决带材单边波浪。
3. 分段冷却控制。通过调整冷却液的分段流量,改变轧辊的局部热膨胀变形。是轧制薄带材的最有效的板形控制手段。
六.提高轧机生产率的手段
AGC系统配置有轧制工艺数据库,可以存储多达几百种轧制工艺。每种轧制工艺包括:轧制道次、入口厚度、出口厚度、卷材宽度、合金号、辊缝、轧制力、轧制速度、入口张力、出口张力、弯辊力和一些控制参数。在轧制不同规格和带材时,只需要调出相应的轧制工艺即可在每次开始轧制以前自动设置轧制状态。
轧制工艺数据库的建立可以采用人工经验的方法,也可以使用轧机数学模型通过软件计算建立。系统中的轧制工艺计算软件可以快速计算轧制道次、辊缝、轧制力、轧制力矩等多种参数,对于频繁变换轧制工艺的小批量、多规格的轧制情况非常有用。
另一方面,在轧制开始以前的准备阶段,系统以带卷号作为标志,将每班的生产计划建立一个轧制队列,根据轧制队列系统自动选择所设定的轧制工艺作为此道次的设定值,实现轧机的自动设定。这样可以减少道次间的辅助时间,提高生产率。
从提高轧机的成材率出发,在控制系统中设置有:
1) 自动加减速控制:在每一道次结束时,为避免轧机轧过轧痕,都要提前减速,在人工控制情况下,有时很难准确判断开卷机上剩余的带材长度,尤其是在轧制薄带材时,为保险起见,势必要提前减速,结果使超差带材的长度加长,减速时间加长,影响轧机的成材率和生产率。自动加减速控制不仅可以完成自动的加速和减速,更重要的是实现了轧机的准确停车,准确停车精度可以做到40㎜。
2) 加减速补偿控制:在轧机的加减速段,轧机出口厚度会随轧制速度的变化而变化,出口厚度将严重超差,加减速补偿控制将根据轧机数学模型来实时调整辊缝或轧制压力,以补偿进厚度的变化,减少轧机加减速段的厚度误差。
七.数据显示和报表记录
在过程管理机及各显示操作站上均设计有丰富的人机接口画面,可实时显示轧机的各种参数和参数变化曲线,并可在轧制过程中修改这些参数。
在每卷带材及每道次轧制结束后,系统可以自动产生带卷报表,记录此卷带材每一道次的轧制情况。包括:辊缝、轧制力、轧制速度、入口及出口张力、弯辊力、入口及出口厚度曲线、厚度偏差分布曲线、产品精度等轧机主要参数。在每一班和每一天生产结束以后,系统可以自动产生班报表和日报表,记录生产情况。带卷报表和班报表、日报表将保存在生产报表数据库中。在数据库中,用户可以根据生产日期、带卷号、班组号、产品规格进行查询,找出所需要的带卷数据,进行质量的跟踪分析,是提高产品质量的有效手段。
八.故障诊断和远程诊断
一个控制系统的可靠性由两个方面来保证:一是系统的平均无故障时间,这可以通过选择高可靠性的元器件及性能先进的计算机来保证;二是系统的故障修复时间,故障修复时间当然是越短越好。AGC故障诊断系统提供了大量的系统保护、检测和报警手段,在故障发生时系统可以自动记录故障发生的原因、发生的时间,用以帮助现场技术人员快速查找系统中发生的各种故障,快速排除。
在轧机现场运行的计算机还可以通过调制解调器MODEM和公用电话网与我们的远程诊断服务器联接,实现远程诊断。诊断服务器中保存有每台轧机的数据,一旦连成功,在诊断服务器上可以看到轧机的实时状态。同时系统留有扩展的余地,可以板形仪等设备或工厂管理机联网。
九.结束语
AGC轧机控制系统是我们重新设计的最新控制系统,它建立在性能先进的计算机和网络基础上,采用美国微软公司最先进的网络操作系统和开发软件,设计了功能强大的应用软件系统,实现全数字厚度和板形控制。它与轧机PLC和传动系统配合,可构成先进的轧机整体自动化系统。AGC系统可靠性高、易维护、操作灵活、控制精度高、软件系统完善,控制指标已达到进口厚控系统的水平,不仅可用于单机架冷轧机、热轧机,也可应用于冷、热连轧机,是新轧机和轧机改造的理想选择。
|
|
|
点击数:1493 录入时间:2012/1/31 【打印此页】 【返回】 |
|
|
|
|